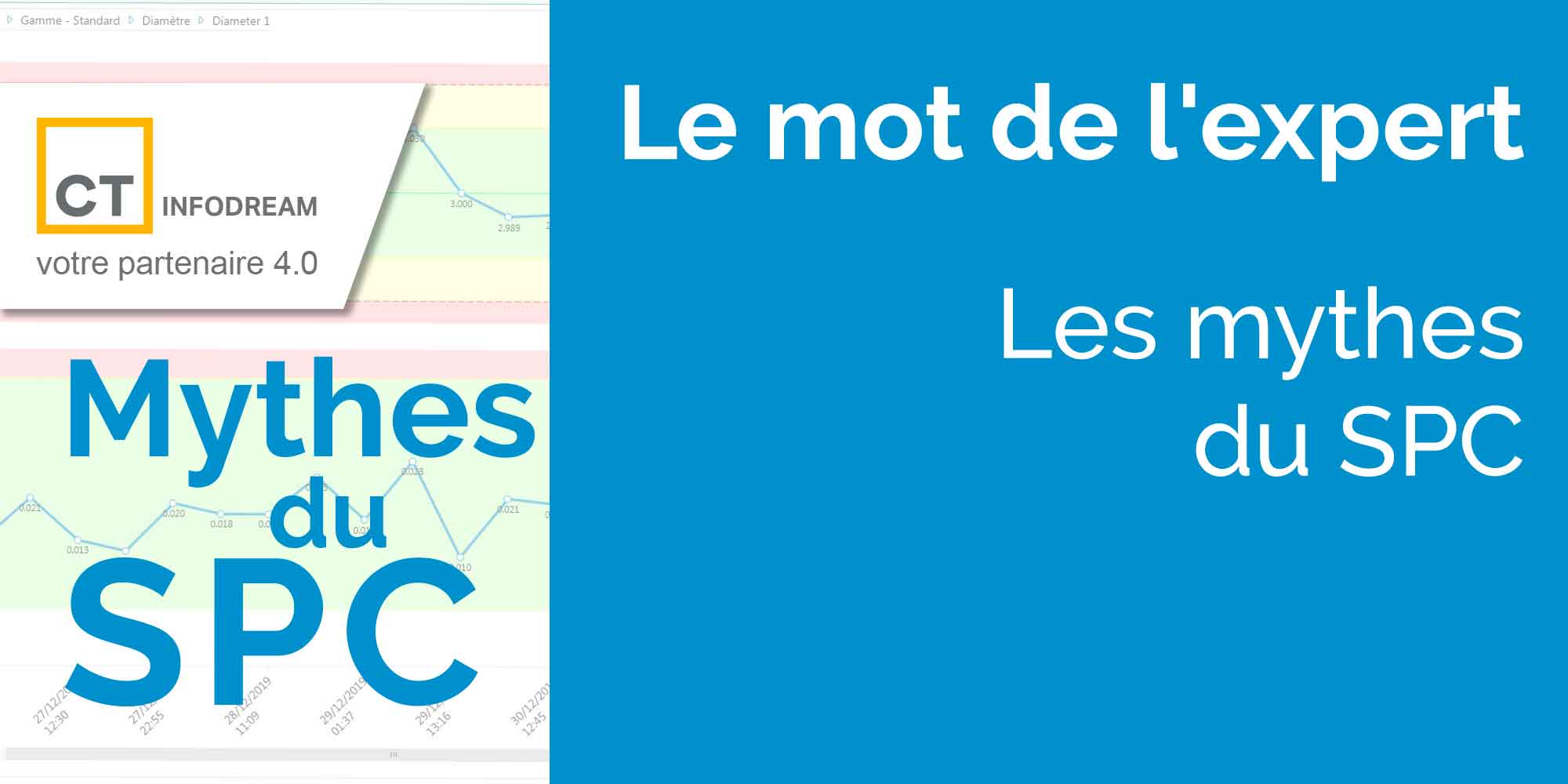
Les mythes du SPC
Statistique ? C’est compliqué !
Et bien non, l’application des statistiques est transparente car complètement gérée et prise en compte par le logiciel ! Le logiciel permet de calculer les indicateurs et de déclencher les alertes. L’outil informatique n’est qu’une étape dans la mise en place d’une démarche complète de SPC. Cette démarche nécessite l’implication de tous (direction, production, qualité, méthodes,…) !
Important : il faut choisir un logiciel suffisamment paramétrable (à tous les niveaux, notamment statistique). L’éditeur du logiciel doit pouvoir également proposer un accompagnement et un support méthodologique pour toutes les phases du projet, pilote comme vie série.
Statistique ? il faut être en grande série !
Et bien non, puisqu’on peut regrouper des références par famille et recréer des effets d’échantillonnage en mutualisant certaines caractéristiques. L’analyse préalable va permettre de regrouper des caractéristiques similaires (au niveau process par exemple) afin de retrouver un effet de série.
Exemple : une pièce aéronautique (petite série) est « pleine de trous ». On va créer un échantillon en regroupant les diamètres mesurés en fonction du diamètre de l’outil, de l’épaisseur concernée et de la matière.
SPC ? C’est une demande client, pas un besoin production !
Et bien non, ce serait dommage ! Ce qui coûte à l’entreprise, c’est la mesure ! Temps de contrôle, instrument de mesure, formation des opérateurs ou des inspecteurs, gestion documentaire des gammes de contrôle… Une fois que la mesure est effectuée et stockée, elle va effectivement générer un histogramme de distribution, des indicateurs et un PV de résultats à destination du client. Mais pourquoi ne pas se servir de cette mesure obtenue en temps réel, au fur et à mesure de la production, pour obtenir des informations utiles pour le réglage et le pilotage du procédé de fabrication?
Point méthodologique : la même mesure effectuée en atelier permet de construire deux visions SPC complémentaires : une vision producteur (fabriquant) avec cartes de contrôle et alarmes, et une vision client final, avec histogramme et indicateurs de capabilités. Si ma carte de contrôle est correcte (mon procédé est sous contrôle), le bilan final (statut du client) sera conforme !
SPC ? C’est pour l’usinage !
Et bien non, la méthode s’applique à tous les procédés de fabrication sur lesquels on peut agir, que l’on peut régler. L’usinage est historiquement concerné, car on a des actionneurs et des correcteurs d’outils, mais des leviers d’action existent sur tous les process :
- température, pression, niveau de vide pour fours, étuves
- temps de repos, °t de stockage pour matériaux composites
Point méthodologique : avant même de donner des règles et indications de pilotage, un système SPC permet de conserver une image (un historique) de la production. Cette notion est évidemment applicable à toute fabrication, automatisée comme manuelle, grande comme petite série…
SPC ? C’est pour les grandes sociétés !
Non, dès qu’il y a de la production, le SPC va apporter tout de suite de la connaissance et des règles de décision.
Un projet SPC est un projet transverse, structurant, qui fait travailler ensemble les Méthodes, la Qualité, la Production, la Direction Générale, le Bureau d’Etudes,… Dans certaines sociétés à taille humaine, ces fonctions peuvent ne pas être découpées aussi clairement, ou une même personne être en charge de plusieurs domaines (méthodes et qualité production par exemple), mais le périmètre du projet reste le même : on veut maîtriser l’ensemble du process de fabrication.
SPC ? C’est ponctuel !
Et bien non, il ne faut pas arrêter le suivi SPC dès qu’on a réglé son problème !
On peut mettre en place une phase 1 de projet afin de diagnostiquer et définir les actions d’amélioration, avec des règles contraignantes et une réactivité demandée importante.
Si le procédé est amélioré et stabilisé, les cartes de contrôle permettront de valider et de quantifier cette amélioration. On pourra ensuite passer en phase 2 et alléger le contrôle ou certaines règles, mais on continuera toujours à vouloir une vision statistique (sur un ensemble de pièces) pour assurer la maîtrise du procédé. Si le procédé dérive, on doit être averti immédiatement, quitte à réactualiser la phase 1 permettant un diagnostic précis !
Point méthodologique : on parle de dérive, mais c’est la même chose si le procédé s’améliore et qu’on ne le détecte pas ! On ne sera pas capable d’identifier ce qui a permis l’amélioration, et donc incapable de le pérenniser. « Que le procédé tombe en panne, ou tombe en marche, on doit être averti de l’évolution ! »
Conclusion
Les quelques points listés ci-dessus sont des idées reçues trop souvent entendues. Un projet SPC bien mené et bien suivi permet toujours de progresser. Suivant les situations, on peut obtenir un ROI quantifiable (par une baisse de rebuts ou de retouches), une meilleure connaissance de ses process et une communication transverse sur des problématiques de production.
Frédéric Henrionnet
CT Infodream