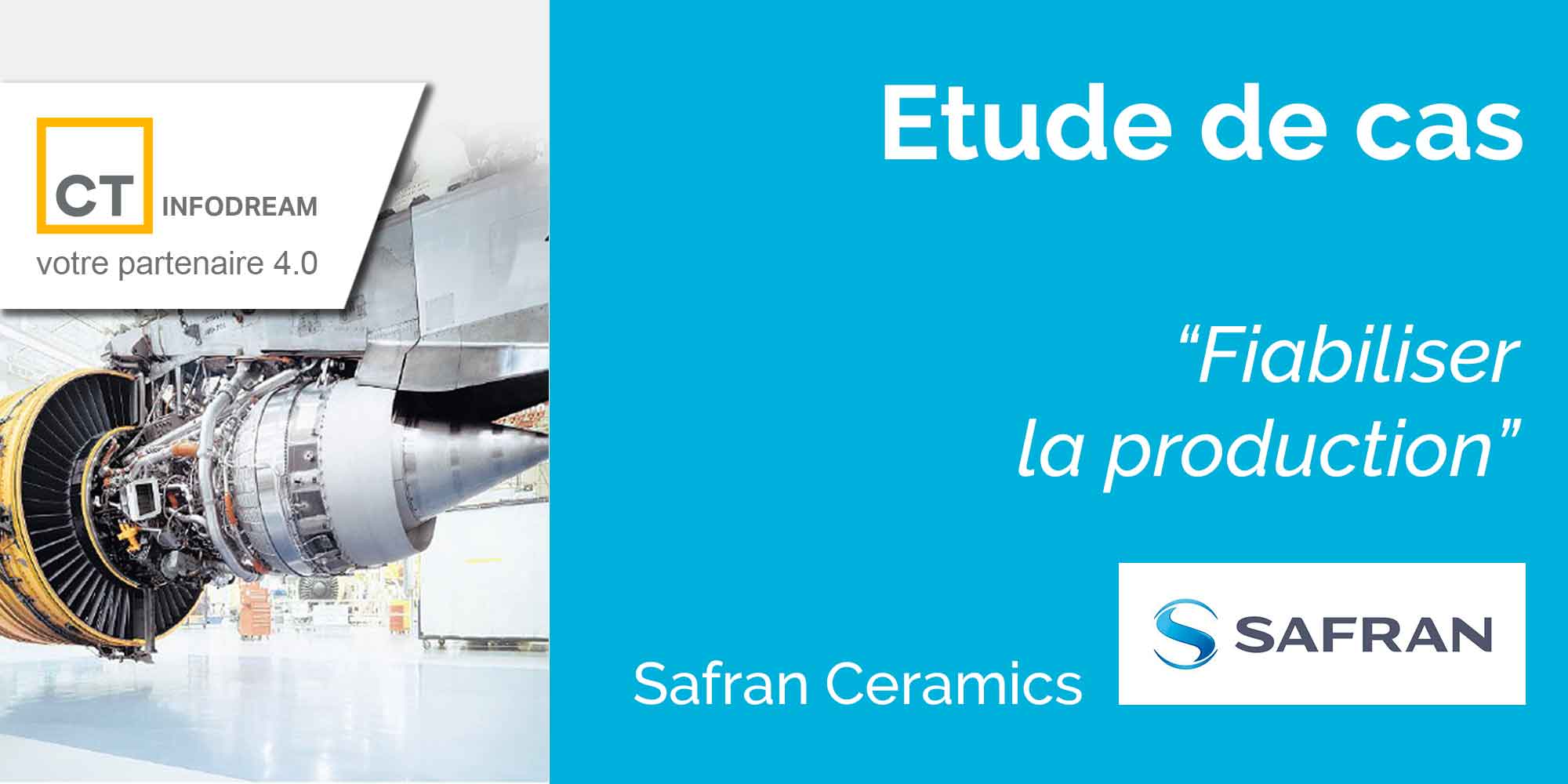
Safran Ceramics fiabilise sa production avec le M.E.S de CT Infodream
Gérer les évolutions
des gammes de fabrication
Fiabiliser les données
et la production
Disposer d’un suivi
de fabrication instantané
Se connecter
aux logiciels existants
Rendre les équipes
autonomes sur le logiciel
Donner aux opérateurs
un outil pour les guider
Fiabilité des données
et qualité des produits accrues
Suppression du papier
dans l’atelier
Communication facilitée
entre les équipes
Qui est Safran Ceramics ?
Centre d’excellence de Safran sur les matériaux composites hautes températures, Safran Ceramics est un centre stratégique pour les travaux du Groupe Safran dans le domaine des équipements aéronautiques.
Découvrez dans cette étude de cas comment Safran Ceramics parvient à fiabiliser sa production avec le M.E.S de CT Infodream.
Installé au Haillan (banlieue bordelaise) dans un nouveau bâtiment de 9800 m2 complètement connecté, Safran Ceramics est un centre moderne regroupant l’ensemble des activités de R&T dédié aux composites à matrice céramique (CMC*) pour l’aéronautique.
Les CMC permettent d’améliorer la performance donc de réduire la consommation de kérosène des moteurs d’avion. En effet ces matériaux tolèrent des températures de fonctionnement plus élevées que les alliages métalliques actuels (superalliages), et sont plus légers.
Dans cette étude de cas nous allons voir comment Safran Ceramics fiabilise ses données, et donc sa production, en utilisant le M.E.S de CT Infodream.
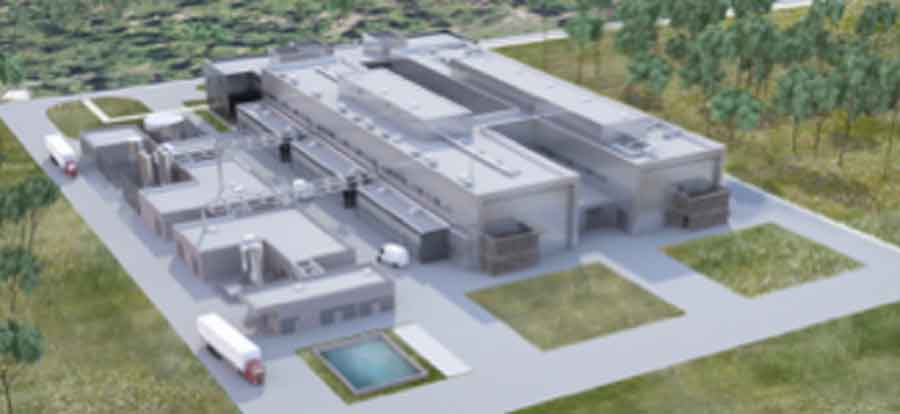
L’usine accueille une centaine de spécialistes répartis en équipes pluridisciplinaires, et 200 équipements de recherche de très haute technologie. Ces équipements, dont certains uniques au monde, sont tous interconnectés pour une acquisition en temps réel de l’ensemble des données de recherche, atout indispensable à l’accélération de l’innovation et au travail agile des équipes.
Chez Safran Ceramics, les employés sont répartis dans 3 départements :
– Etudes et modélisations
– Matériaux, procédés et essais
– Technologies et Ingénierie de production : fabrication et développement des moyens de production.
C’est dans ce service qu’a été implémenté le MES.
Les travaux réalisés au Haillan se situent en amont des phases de développement, d’industrialisation et de production qui seront réalisées dans les autres sociétés du Groupe.
Les produits réalisés sont principalement des pièces de turbine (aube et distributeur) et des arrière-corps (tuyère, mélangeur et cône d’éjection).
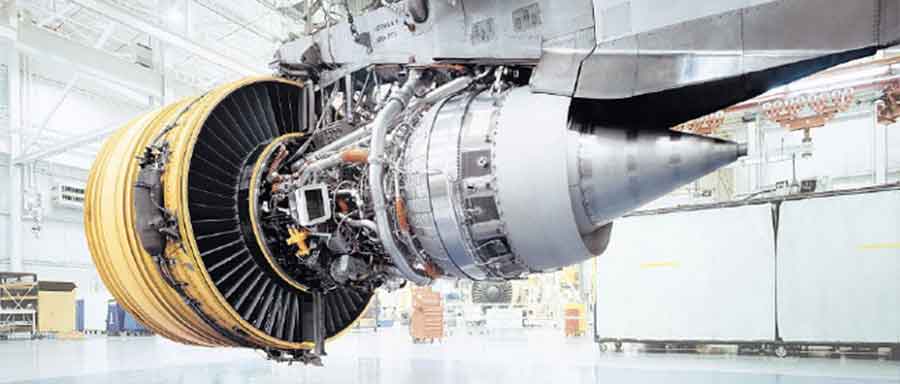
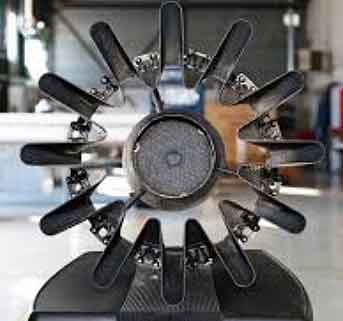
Quels étaient les besoins de Safran Ceramics ?
Safran Ceramics souhaitait :
- supprimer le papier dans l’atelier.
- gérer des évolutions de gamme.
- fiabiliser les données et disposer d’un suivi de fabrication instantané.
- faciliter la communication entre les équipes.
- garantir la qualité des produits auprès de nos clients.
Supprimer le papier dans l’atelier.
Avant, les instructions de travail et les fiches de suivi de fabrication étaient conçues sur fichiers Word, puis imprimées.
Les données récoltées dans l’atelier étaient écrites sur feuilles volantes par les opérateurs puis saisies sur fichier Excel.
Il y avait donc un besoin de digitalisation (disposer de gammes -processus- avec des instructions de travail et des fiches de suivi de fabrication numériques).
Gérer les évolutions de gamme.
Les processus, parfois longs et complexes, pouvant évoluer en cours de la fabrication, il fallait pouvoir modifier les gammes à la volée.
Fiabiliser les données et disposer d’un suivi de fabrication instantané.
Les fichiers Excel pouvaient être ouverts et modifiés par différentes personnes sans traçabilité, avec les risques d’erreur que cela implique.
Il fallait aussi s’assurer de la cohérence des informations entre les méthodistes et les opérateurs de l’atelier, de façon à ce que chacun dispose bien des mêmes informations, et que celles-ci soient à jour.
Enfin, il n’était pas toujours évident de savoir qui avait fait telle modification, quand et pourquoi, 3 types de personnes étant habilitées à faire des modifications :
- Le pilote industriel (le chef d’orchestre) pour chaque gamme / processus.
- Les méthodistes
- Le service qualité pour contrôler les changements de version
Faciliter la communication entre les équipes.
Pour se transmettre les informations, les déplacements entre les bureaux et l’atelier étaient une perte de temps non négligeable pour les équipes.
Garantir la qualité des produits auprès de nos clients.
Les pièces produites par Safran Ceramics sont envoyées et testées sur banc d’essai chez les clients (d’autres entités du Groupe Safran). Ces tests sont longs et coûteux, il faut donc être sûr que les pièces envoyées répondent à certains critères qualité.
Comment Safran Ceramics a-t-elle connu CT Infodream ?
Par la réponse de CT Infodream à un appel d’offre. D’autre part, le responsable de production connaissait déjà la Suite Qual@xy et ses possibilités. C’est d’ailleurs lui qui a été moteur sur le projet après que le choix d’Infodream ait été fait.
Pourquoi avoir choisi CT Infodream ?
Parmi les répondants à l’appel d’offres lancé par Safran Ceramics, un audit a été réalisé.
Les éléments différenciant qui ont orienté notre choix sont :
- La simplicité de la solution
- L’autonomie permise par le logiciel
- Le prix
La simplicité
La première caractéristique recherchée était la simplicité. Sans service dédié pour installer l’outil et former les collaborateurs, il fallait une solution clé en main, simple à mettre en place, à configurer et à utiliser.
Simple pour être souple. Souple pour plus de liberté et d’autonomie.
L’autonomie
Les méthodistes disposent d’une grande latitude dans la modification des processus. Ils n’ont pas besoin d’accompagnement. La formation initiale leur a montré comment utiliser l’outil, comment paramétrer le produit et le processus. C’est très simple, aucun développement informatique n’est nécessaire pour modifier un processus, tout se passe au niveau du paramétrage.
Dès lors qu’on fournit un outil simple aux opérateurs, ils l’adoptent rapidement et l’utilisent réellement au quotidien.
Le prix
Enfin le prix a été également un critère différenciant, avec un facteur 3 par rapports à certains concurrents dont la solution nécessite la présence permanente d’une personne pendant plusieurs jours pour la mise en place, le paramétrage et la réalisation des ajustements nécessaires. Et cela a un coût…
Le choix a été fait de façon collégiale avec le responsable du service production, le responsable support et le responsable des autres services.
Comment s’est passé la mise en place de la solution ?
La mise en place de la solution s’est déroulée sans problème.
Pendant la phase de déploiement, un ordinateur dédié a été mis à disposition pour communiquer avec Infodream. Une base de données de tests a été installée pour configurer les gammes en toute sécurité avant le passage sur la base de production.
Les méthodistes, moteurs sur le projet, ont été les premiers formés et ont pu participer à la formation des opérateurs.
Combien de temps a-t-il fallu pour la mise en place de ce projet MES ?
Il a fallu un an entre le choix de la solution et la mise en production.
Quelles ont été les difficultés rencontrées ? Et comment ont-elles été surmontées ?
Il n’y avait pas de logiciel MES auparavant. La principale difficulté du projet était de se connecter aux autres logiciels existant chez Safran Ceramics :
- Smarteam, pour la conception, le nom des produits et des versions ;
- Historian, pour l’enregistrement des données de production relatifs aux OF ;
- Carl Source pour la disponibilité des machines ;
- SAGE pour l’ordonnancement, le suivi du planning et le lancement des OF.
Il fallait donc connaître l’environnement de chacun de ces logiciels pour permettre à Qual@xy de s’y connecter.
Ce n’était pas tant une difficulté d’ordre technique (le M.E.S Qual@xy est conçu pour se connecter aux machines et logiciels existant dans l’usine) que logistique. Il fallait se mettre en relation avec les représentants techniques de ces sociétés, organiser des réunions de travail communes sur les agendas de chacun pour faire avancer les choses rapidement.
Le POC (Proof of concept), quant à lui, a été rapidement mis en place.
Comment les équipes ont-elles été préparées au changement ?
Par la sensibilisation et la formation des configurateurs. Ce sont d’ailleurs les configurateurs eux-mêmes qui ont assuré la formation des opérateurs.
Comment ont-elles accepté ce nouvel outil ?
Très positivement. Les collaborateurs disposent de gammes à jour, et cela leur évite de faire deux fois l’enregistrement des données. L’interface est conviviale et les équipes trouvent le logiciel facile à utiliser.
Quels profils d’utilisateurs travaillent avec l’outil ?
Des ouvriers, techniciens et ingénieurs.
Etes-vous autonome sur la configuration ou les modifications du logiciel ou faites-vous appel à CT Infodream ?
Nous sommes globalement autonomes, mais parfois nous faisons appel au pôle support de CT Infodream.
Par exemple pour des questions relatives à la configuration des gammes ou des choses vues en formation mais qui, faute de pratique, ont été oubliées.
Votre avis sur le pôle support de CT Infodream ? Sur le suivi de projet de nos équipes ?
Le support est toujours disponible, a une réactivité haute et les solutions sont adaptées.
J’ai été étonné ! Les gens sont disponibles, intéressés, consultent le PC mis à disposition pour analyser les données et proposent toujours, après concertation, une solution adaptée.
Ils nous ont donné la bonne méthodologie pour configurer les gammes de contrôle.
Franck Dupé, ingénieur informatique
Quels sont les bénéfices de l’utilisation du M.E.S (Manufacturing Execution System) ?
Ils sont nombreux, mais voici les principaux :
La collecte des données et l’identification de l’impact du changement de paramètres
Maintenant, les informations, mesures ou traçabilités sont saisies directement dans le logiciel. A l’usage, on s’aperçoit que cela permet de collecter beaucoup plus d’informations qu’avant tout au long du processus de fabrication.
Les départements production et matériau ont à disposition avec cet outil une base de données riche permettant d’identifier l’impact de la modification de chaque paramètre sur la qualité du matériau.
Un stock de données est ainsi constitué avec un moindre effort et pourra faire l’objet d’analyses ultérieures en cas de besoin.
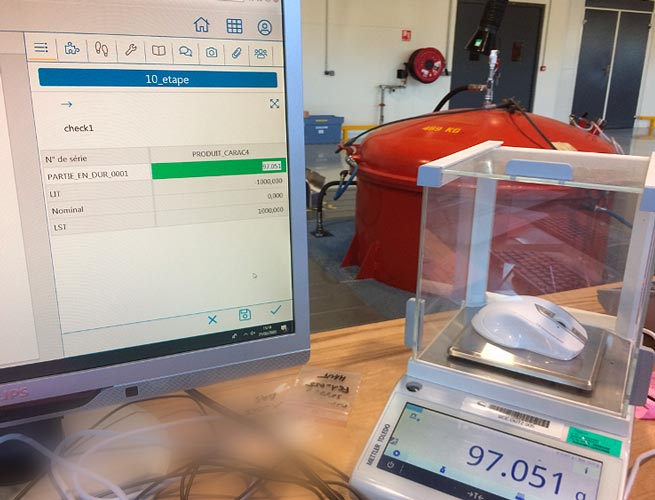
La modification des gammes en quelques clics
Les méthodistes, grâce à la souplesse de l’outil, peuvent modifier les gammes en quelques clics, même en cours de fabrication ! Et tout cela est tracé, le M.E.S Qual@xy permettant de suivre toutes les évolutions grâce à l’utilisation du versioning (gestion des workflows de validation).
La communication grandement facilitée
Autre point positif : le MES facilite la communication entre les équipes en faisant le lien entre les méthodistes et les opérateurs. Maintenant l’atelier dispose d’informations fiables mises à jour par les méthodistes. Les données sont instantanément transmises et visibles par chacun.
Inversement l’atelier renseigne des données consultables en temps réel par les méthodistes. Chacun peut suivre les évolutions et consulter les données saisies.
Le flux d’information fonctionne dans les deux sens, ce qui facilite la communication et évite les déplacements superflus entre bureaux et atelier.
Des rapports prouvant la qualité des pièces livrées.
Les pièces envoyées chez les clients répondent aux critères qualité qu’ils exigent, et la preuve peut maintenant leur être apportée ! En effet le MES permet d’extraire des rapports ciblés sur certaines valeurs de chaque pièce.
Ces rapports feront office de bons de livraison et accompagneront les pièces tout au long de leurs phases de tests.
En résumé, cette étude de cas montre les principaux avantages à l’utilisation du M.E.S :
Pour Safran Ceramics : la production est fiabilisée
Pour les opérateurs : la mise à disposition d’un outil dédié pour les accompagner dans leur travail
Pour les managers : l’assurance d’une bonne adéquation entre le besoin et le produit.
On sait ce que l’on fait et le produit répond bien aux attentes initiales.
Franck Dupé,
Ingénieur informatique chez Safran Ceramics
*CMC : composites à matrice céramique
Il s’agit de céramiques renforcées par des fibres également en céramique qui permettent de leur ôter leur fragilité naturelle. Ces matériaux se démarquent des alliages métalliques habituellement utilisés dans l’industrie aéronautique par leur résistance aux fortes températures, leur légèreté et leur tenue mécanique. On distingue différents types de CMC selon la nature chimique de leur matrice et de leurs renforts : les CMC à base de carbone, de carbure de silicium ou d’oxydes.
Ces témoignages de nos clients peuvent aussi vous intéresser…
Lynred – logiciel SPC
Pour LYNRED, l'amélioration continue est une route sans fin… Ou comment LYNRED améliore constamment ses procédés de fabrication avec le logiciel Qualaxy SPC. Qui est LYNRED ? LYNRED et sa filiale américaine LYNRED USA sont leaders mondiaux dans le développement…
Ventana a pu identifier des axes d’amélioration sur ses process
Dans cette vidéo d’1 min., l’opérateur explique comment il utilise notre module de digitalisation de processus de la Suite Qualaxy (M.E.S)
Tronics apporte de la rigueur dans le suivi de son outil industriel.
Tronics Microsystems implémente l’outil Qualaxy Process pour la gestion de son usine de Crolles. Créée en 1997, Tronics (Crolles, 38) est spécialisée dans les nano et microsystèmes innovants, (NEMS et MEMS) : ces dispositifs miniaturisés assurent des fonctions de capteurs…
Mölnlycke Health Care
Nous pouvons maintenant nous réjouir de l’efficacité accrue et de l’énorme économie de temps - ce qui, tout simplement - n’a pas de prix. Jacques MARIN Mölnlycke est l'un des principaux fournisseurs mondiaux de produits à usage unique pour…
Airbus Helicopters
Après le déploiement de Qualaxy SPC pour son activité Qualité dans la fabrication des Pièces Elémentaires Mécanique (plus de 100 postes déployés à ce jour dans l’atelier), Airbus Helicopters à Marignane avait besoin d’une solution de Management du Processus de…
Safran Helicopter Engines
Safran Helicopter Engines (UK) est spécialisée dans la fabrication d'ensembles mécaniques complexes destinés à l'industrie aéronautique. Cela concerne aussi la maintenance, réparation et révision des turbines à gaz de petite et moyenne dimension. La société fait partie du groupe SAFRAN,…
Safran Aircraft Engines
Le site Safran Aircraft Engines à Evry-Corbeil regroupe 3 200 salariés sur 56 hectares ; il dispose d'un atelier de 88 000 m² et d'un parc de plus de 400 machines dont près de 290 à commandes numériques, pour plus…