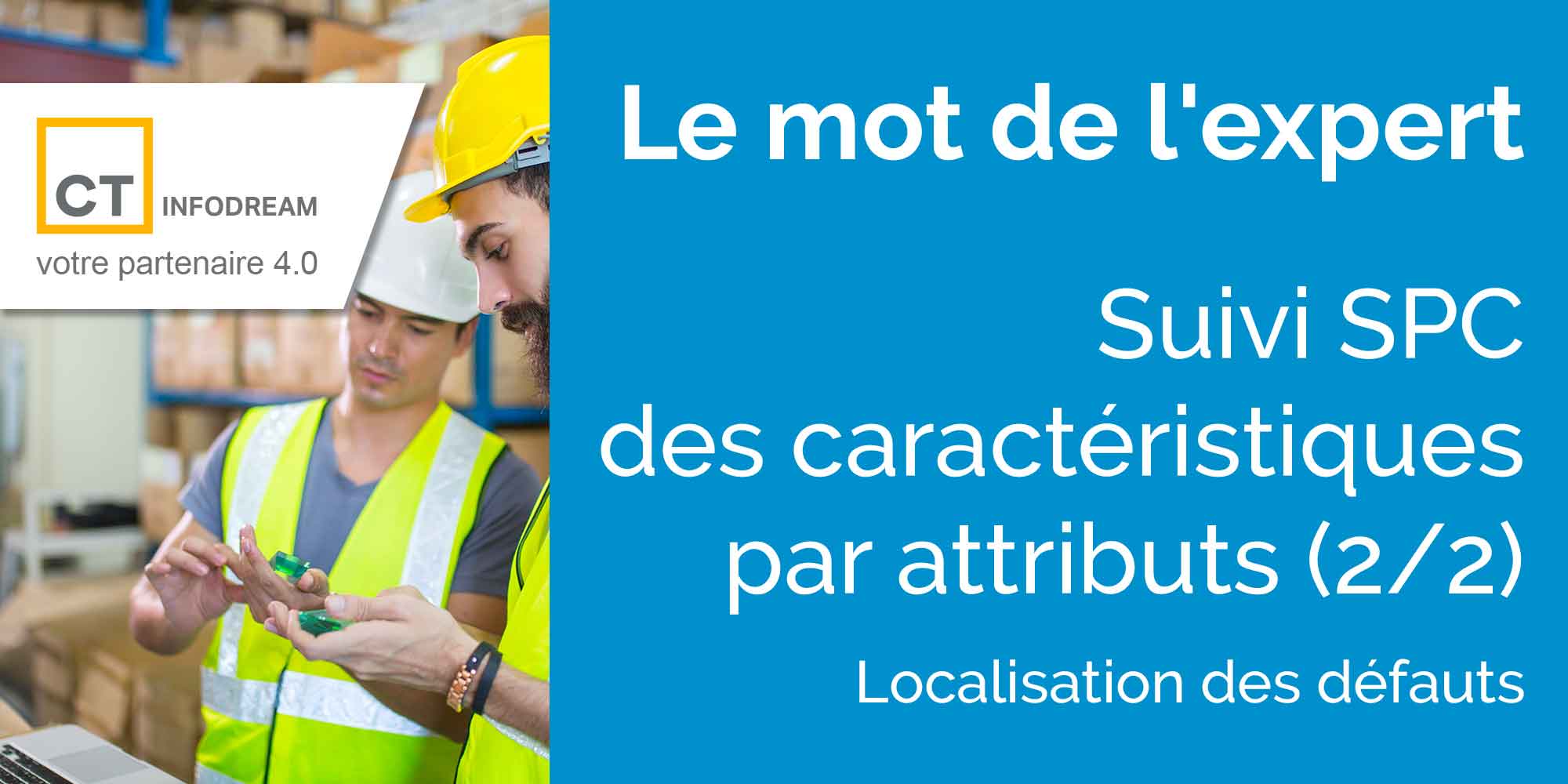
Defect Map – un contrôle attributif introduisant la notion de localisation des défauts (2/2)
Le contrôle attributif des défauts d’aspect
Le contrôle attributif des défauts d’aspect dans une approche SPC se fait en utilisant les cartes classiques de suivi des attributs NP (nombre de pièces non-conformes), C (nombre de non-conformités), P (proportion des pièces non conformes) ou U (proportion de non-conformités par unité).
Si on utilise une carte C pour des pièces à haute valeur ajoutée en contrôle 100%, on va suivre l’évolution du nombre des défauts pièce par pièce. Dans certains cas, ce suivi est suffisant. Par contre, on peut imaginer d’autres cas pour lesquels l’information sur le nombre des défauts n’est pas suffisante.
Pour pallier ce manque, la notion de localisation des défauts (ou defect map) peut être introduite pour des contrôles attributifs. Au lieu de renseigner seulement la présence du défaut, on va également documenter l’endroit où il se situe sur la pièce.
L’image ci-dessus montre une application possible bien connue d’un suivi attributif utilisant une cartographie des défauts. Sur l’image, un loueur de voitures renseigne les défauts rencontrés au moment où un client retourne sa voiture de location. Sur cet exemple, le loueur constate deux défauts : un premier défaut sur le capot, un deuxième défaut sur l’aile avant gauche.
Dans le domaine industriel, on peut imaginer une multitude d’applications qui nécessitent de connaître la localisation des défauts, pour pouvoir prendre la décision de rebuter une pièce ou non.
Dans l’aéronautique, on accepte éventuellement une fissure qui se trouve dans une zone de faible sollicitation physique. Par contre la même fissure entraine le rebut de la pièce si elle se trouve dans une zone qui subit une forte sollicitation.
Pour un fabriquant de montres, une rayure peut être acceptée si cette rayure se trouve dans un endroit non-visible de la pièce finale. Par contre si cette rayure se trouve au milieu de la lunette bien visible pour le client, le même défaut entraine le rebut de la pièce.
Les exemples cités ci-dessus montrent des cas où la localisation des défauts joue un rôle déterminant pour la décision de rebuter ou non une pièce. On peut également imaginer des cas pour lesquels des informations supplémentaires pour le défaut (longueur du défaut, surface du défaut) sont importantes pour la prise de décision.
Comme pour sa localisation, on pourrait demander de préciser chaque défaut par un nombre défini d’informations supplémentaires.
Suivant la taille de la rayure ou d’un impact sur son capot, la décision du loueur ne va pas être identique : il peut accepter le retour tel quel ou demander une réparation et faire jouer l’assurance.
Il lui appartient donc de caractériser ces défauts, soit en les classifiant (petit, moyen, gros), soit en les mesurant (rayure de 15mm de long).
Dans certains domaines, une fissure peut être considérée comme acceptable si sa longueur est plus petite que quatre millimètres. Si elle est plus longue, la pièce doit être rebutée. Pour un fabriquant de vitres, une irisation peut être considéré comme non gênante, si sa surface ne dépasse pas 5mm².
Tous ces exemples illustrent la possibilité d’utiliser une Defect Map (cartographie ou localisation des défauts) pour prendre les bonnes décisions au moment où il faut statuer et décider de rebuter ou non une pièce. Si on limite l’utilisation d’une cartographie des défauts à cette aide décisionnelle, on n’observe malheureusement pas de diminution du nombre de défauts.
Comment peut-on profiter de ces informations supplémentaires (localisation des défauts et caractérisation) pour contribuer à faire diminuer le nombre de défauts ?
Localisation des défauts : oui, mais comment faire diminuer leur nombre ?
Imaginons que notre loueur de voiture « superpose » maintenant les défauts constatés pour toutes les voitures louées pendant une certaine période. On obtient une cartographie des défauts qui permet de constater dans quelles zones d’une voiture on trouve le plus grand nombre de défauts.
En regardant la localisation des défauts ci-dessus, il pourrait prendre des actions correctives pour limiter le nombre d’impacts dans certaines zones et demander l’installation de radars de recul pour limiter les problèmes sur l’arrière des véhicules !
Reportant cet exemple dans le domaine industriel, on constate qu’avec l’aide de la Defect Map (localisation des défauts), on peut facilement identifier des zones qui présentent souvent des défauts et chercher la cause pour cette accumulation. En éliminant la cause identifiée, on obtient automatiquement une réduction des défauts.
En superposant un lot de production (par ex les 20 pièces de la semaine) on se rend compte qu’on a une zone qui concentre un grand nombre de défauts (R2-S2 à R3-S5) : on ne s’en serait pas rendu compte en examinant les pièces 1 à 1 !
Pour conclure, on arrive à renforcer le côté statistique des cartes aux attributs :
- on ajoute de l’information sur les défauts (ce qui d’obtenir des informations d’analyse plus rapidement, avec un moins grand nombre de pièces)
- en « superposant » les Defect Map des pièces, on se recrée un effet d’échantillon, et on peut se permettre des suivis et des évolutions dans le temps.
Frédéric Henrionnet
Responsable Assurance Qualité, CT Infodream
Andreas Völker
Product Manager, CT Infodream
En savoir plus sur le module Qual@xy SPC
En savoir plus sur la fonction Defect Map